21st May 2021
Food manufacturer, Young’s Seafood Limited, has been fined after a worker was trapped by a mixing machine.
Grimsby Crown Court heard that, on 16 October 2017, the 59-year-old worker was creating the mix for fish cakes at the company’s Humberstone Road factory in Grimsby. At the end of a mix run he went to clear the mix from the machine, lifting an interlocked guard that should have stopped the machine from running. He put his hand into the machine without realising it was still running and the augur caught his hand and drew his arm in up to the elbow. The worker managed to free himself from the augur but in removing his arm, his thumb and two of his fingers were severed and he suffered serious tendon damage. Following the incident doctors were unable to reattach his fingers and he has not yet been able to return to work.
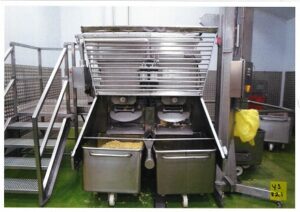
An investigation by the Health and Safety Executive (HSE) found that the machine continued to run when the safety guard was lifted and failed to respond when the emergency stop was pressed. The interlocking system was inadequate, and the company had failed to ensure that the machine was effectively maintained. These matters were exacerbated by poor communication between the shop floor and maintenance and an inadequate fault reporting system.
Young’s Seafood Ltd of Ross House, Wickham Road, Grimsby Lincolnshire pleaded guilty to breaching Section 2 (1) of the Health & Safety at Work Act 1974. The company has been fined £787,500 and ordered to pay £33,443.68 in costs.
After the hearing, HSE inspector Carol Downes commented: “The life changing injuries sustained by the employee could have been prevented and the risk should have been identified.
“Being pro-active with preventative maintenance and good communication of faults can reduce the chance of harm.”
PLUS SAFETY Comment:
A completely avoidable accident highlighting the importance of emergency stop checking procedures to ensure that when you need an emergency stop it actually works! Emergency stop buttons, interlock devices, light curtains, pressure pads and any other safety related device attached to a process to interrupt and stop the operation should be checked for integrity regularly and the result/action recorded. If they are found defective – stop the process and get it fixed! Compare the cost of temporary stopping the process to the cost of a potential accident, in Young’s case how many emergency stop checks would £820,943.68 funded? Its a no brainer, and the poor worker would still have his fingers and thumb!